Technology
We believe that progress lies in modern technologies
Our manufacturing plant has state-of-the-art technology and cutting-edge equipment used only by experienced professionals. Therefore, our clients can always rely on us when it comes to delivering products that meet the highest expectations. What do we specialize in manufacturing?
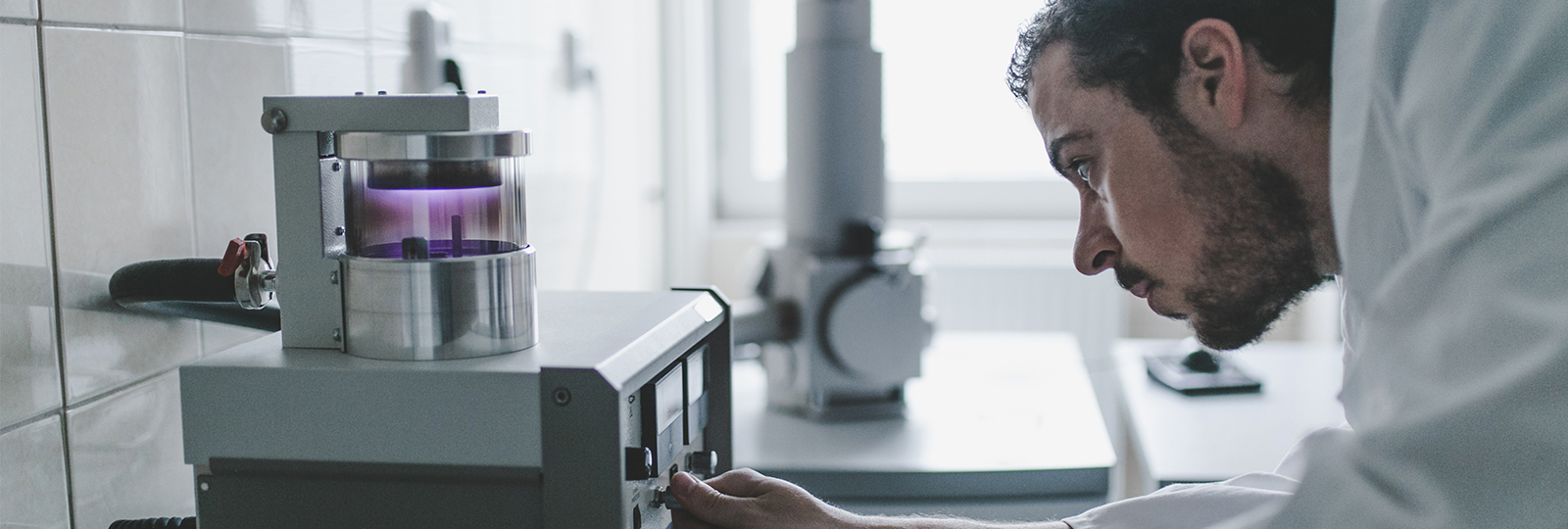
Materials of the future, that is our domain. How does it work?
- First, nanofibers are applied onto a suitable carrier.
- Adhesion of the nanofibrous layer to the substrate must be ensured.
- Fabric materials are connected with nanofibrous layer using powder adhesive.
- Layers of nanofibers with fabric materials are laminated on one side or on both sides.
The barrier fabrics we develop and continually refine are essentially three-layer or multi-layer fabric laminates. Their outer surface is formed by common spunbond or meltblown nonwoven materials, between which we insert a layer of submicron fibers (nanofibers).
Mechanical interconnection of three-layer fabric laminates or two-layer filter media is done by applying adhesive solution on the substrate before covering it with nanofibers, alternatively they can be connected unilaterally or bilaterally with powder adhesive.
We use laminating technologies that help us to extend the application of nanofibrous materials to various industries and final products. Our materials are widely used - they are used in construction, medicine and households.
Critical parameter of usability of filter media with nanofibrous layer is to ensure there is sufficient adhesion between carrier medium and nanofibrous layer. We consistently oversee the coherence of the layers, which fundamentally affects the processability of the media into final products.
Production
technology
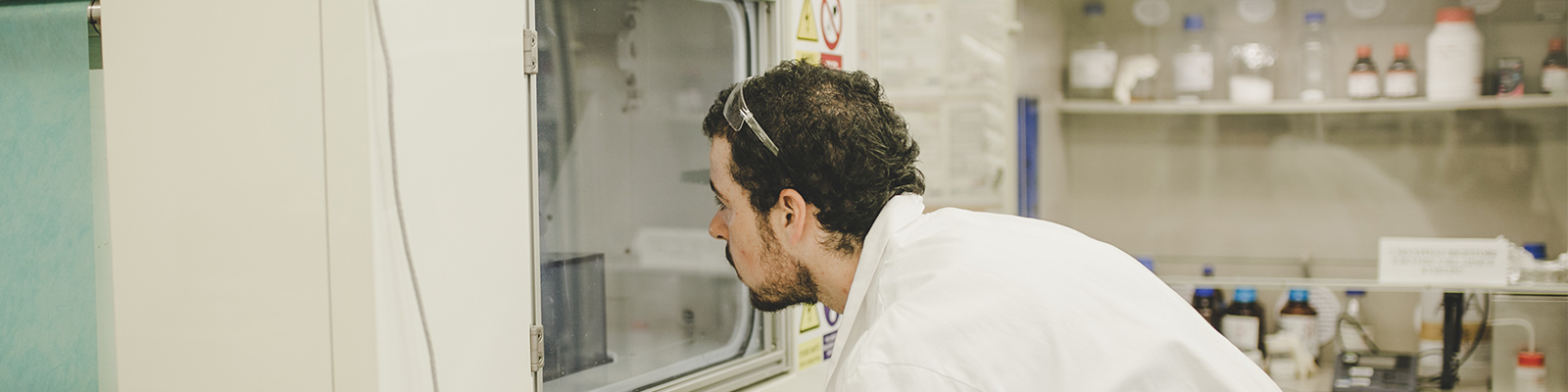
Nanofibers
The nanofibers we work with are thousands of times thinner than the human hair. The usual fibre diameter range is between 100 - 500 nm. Thanks to this, nanofibrous layers have quite unique properties:
- high surface area-to-volume ratio
- high porosity
- small pore dimensions
- possibility of nanofiber additivation, for example by biologically active substances
The principle of barrier fabrics and filter materials containing nanofibers is based on these very properties. The small pore size allows mechanically filtering out dust and biological impurities of very small size, high porosity provides good permeability of these materials for the penetration of air or fluid..
Do you want to learn more? All about nanofiber materials, their applications and research projects undertaken in connection with nanofibers can be found on www.nafigate.com or www.nanoasociace.cz.
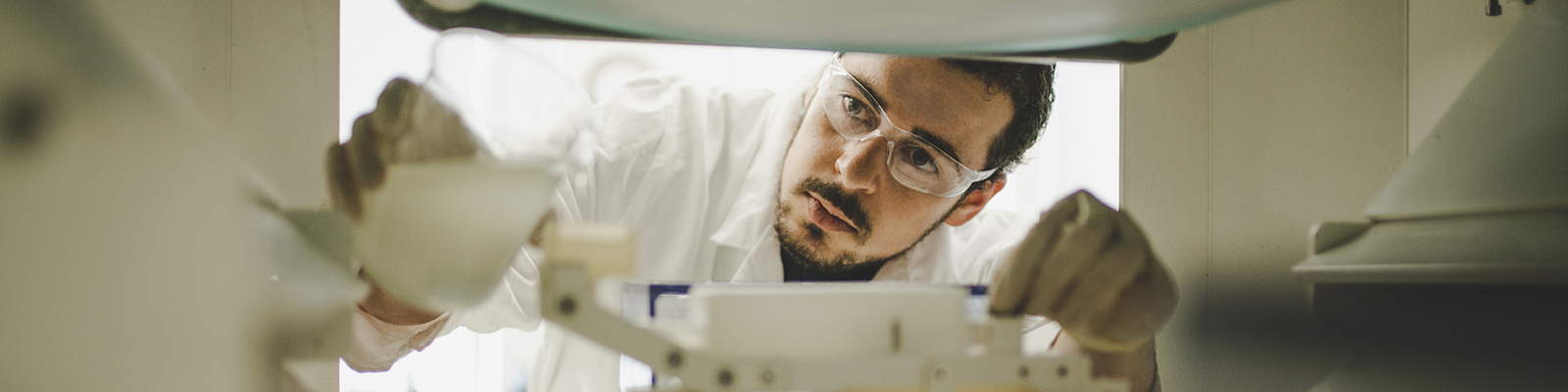
Nanofiber Production
When it comes to production of nanofibers itself, we use Nanospider™ technology based on the principle of spinning the polymer solution in electrostatic field.
We use laboratory machines intended for the development of new materials and preparation of samples. Industrial production of barrier fabrics, filter materials, nanofiber membranes and other nanofiber materials is provided by several industrial machines Nanospider™.
- maximum operating width of 1650 mm, nanofiber layer maximum width of 1600 mm
- maximální zpracovatelný průměr návinu je 1200 mm
- maximum processable winding diameter of 1200 mm
In industrial production of nanofiber materials for barrier fabric and filter materials we use mostly polymers PA6 and PVDF. The production itself takes place in an area of cleanliness class 8 according to ISO 14664 which is part of our production plant.
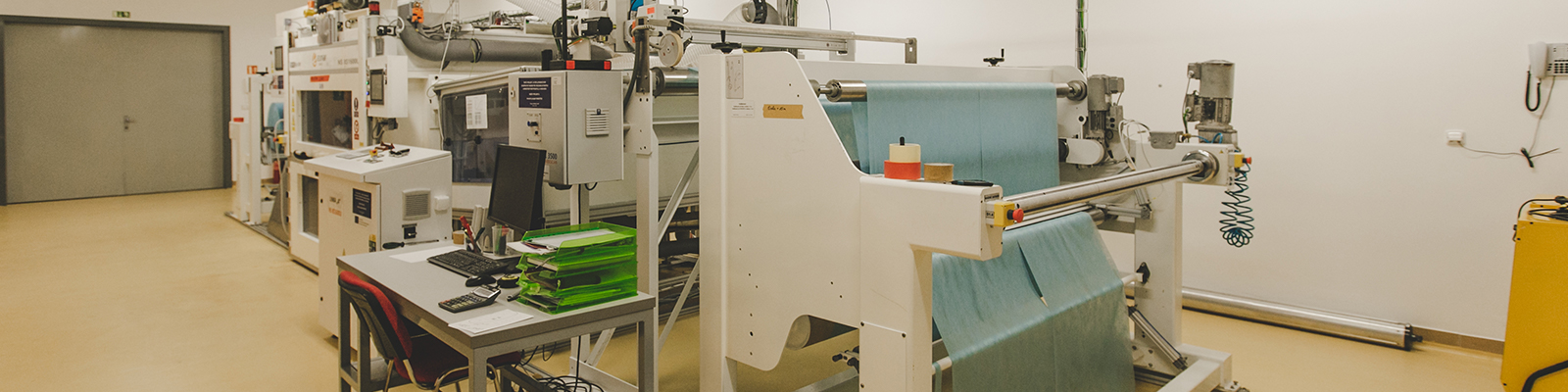
Fabric laminates
Our barrier fabrics and filter media are the three-layer or multi-layer fabric laminates containing at least one nanofiber layer enclosed between the non-woven fabrics or textiles.
Nanofiber layer in our laminates is usually very thin (basis weight of between 0.05 to 1.0 g/m²), therefore it has no sufficient mechanical properties for its handling.
When the nanolayer is fixed to the carrier, its mechanical properties are dramatically improved. However, there is still a risk of damage to the nanostructure during further processing and use. Only the reversible protection of nanofiber layer ensures its mechanical and shape stability and resistance against abrasion during processing and use.
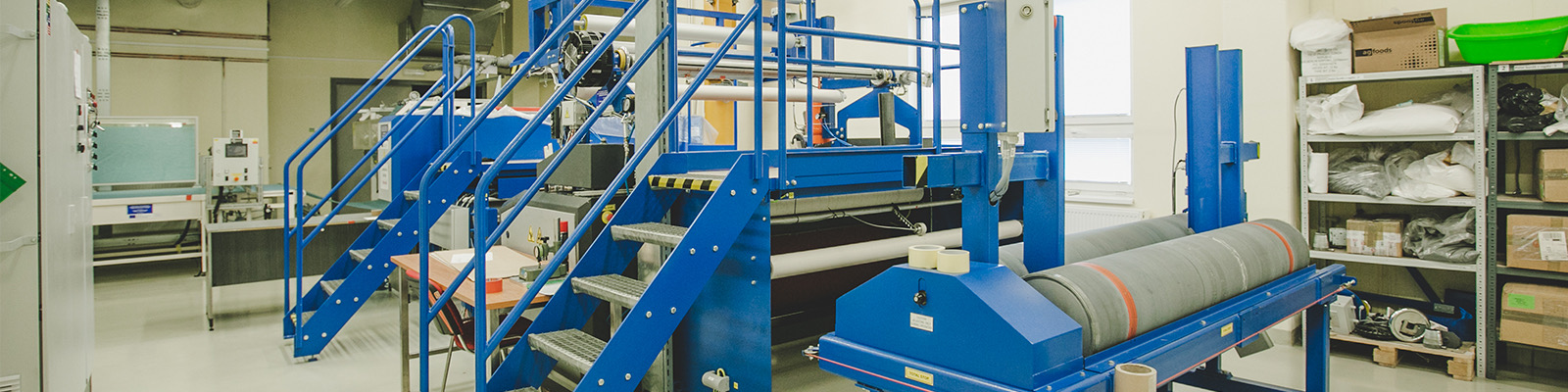
Lamination
We have a technology enabling the application of powdered adhesive granulate 80–200 µm or melt nets. Connecting the layers is done using pressure and temperature.
The Klieverik laminating line allows us to create sandwich-type multilayers and also to separate the product (membrane) from the carrier material in the final step. As a result, we are able to deliver exactly what you require.
Lamination technology operating data:
- maximum operating width of 1800 mm
- maximum processable winding diameter of 1200 mm at the input, 800 mm at the output
- tube diameter at the inlet of 76 mm, at the outlet of 76
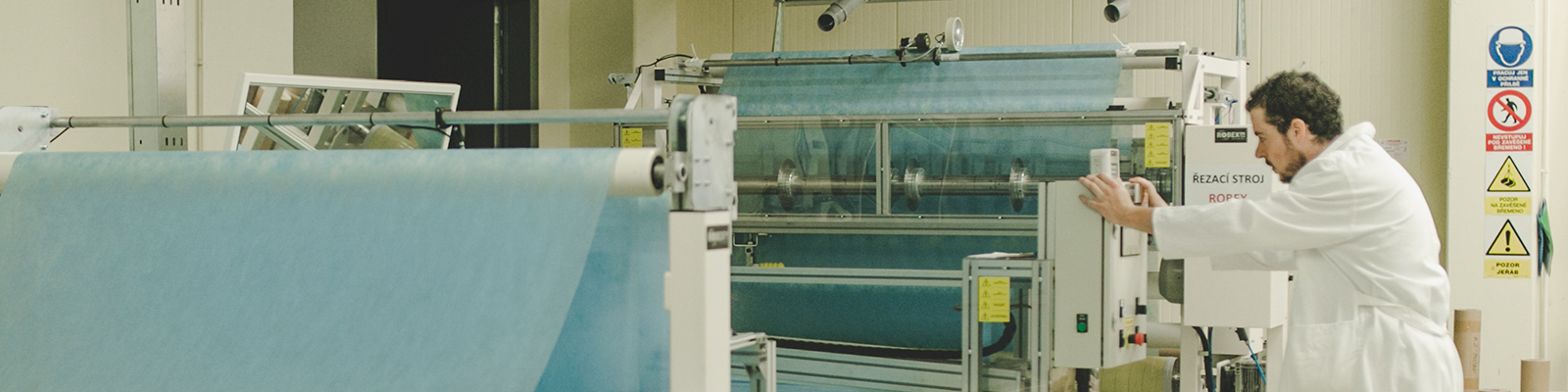
Longitudinal strip cutting
After the material lamination, cutting the edges of laminate and adjusting the material to a final commercial packaging occurs. Should a client require, we can cut the material into stripes of different widths to make its further processing even easier.
Forming technology operating data:
- maximum operating width of 1800 mm
- maximum processable winding diameter of 1200 mm at the input, 800 mm at the output
- tube diameter at the inlet of 76 mm, at the outlet of 76
- minimum strip width of 70 mm
- maximum number of cutting discs 13
- cutting accuracy +/- 1 mm
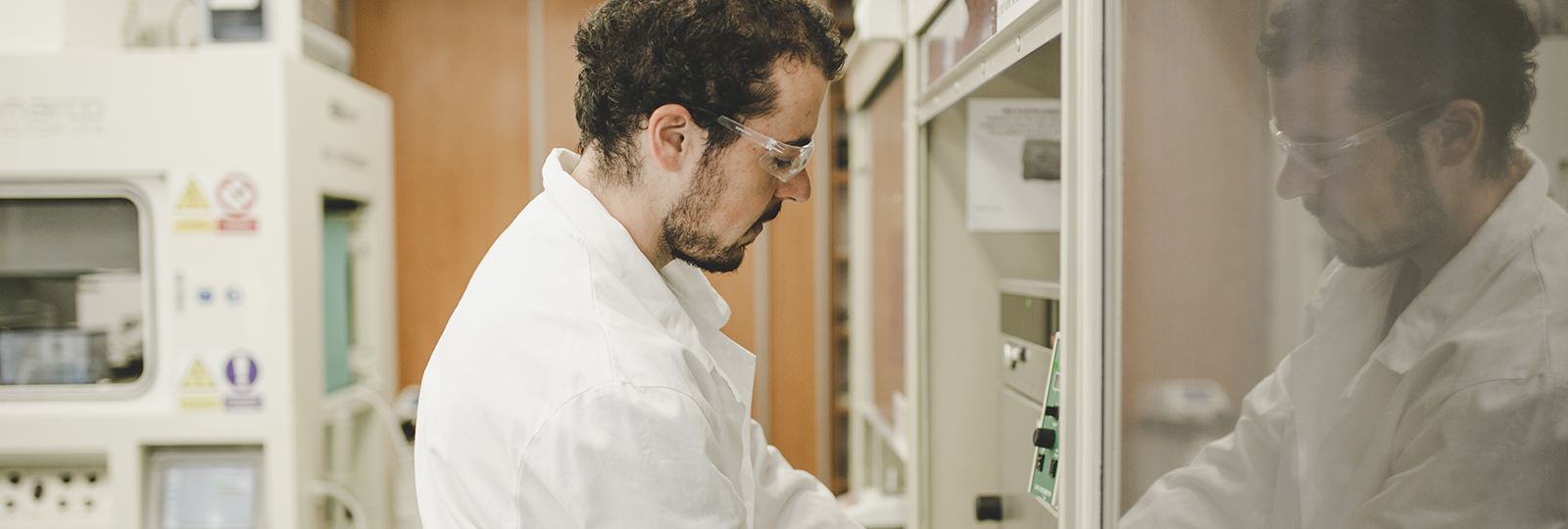
We have our way with technologies
We are engaged in research, development and production of nanofibrous textiles. Our strengths include state-of-the-art laboratories, years of know-how and experienced professionals working for us.
Our mission
Tiny dimension, Huge results
They are so small a naked human eye can hardly see them. Nanofibers are used in industry, healthcare, construction and many other areas. We thrive on utilizing their unique features to the full potential, so the life can be a little easier for all of us.